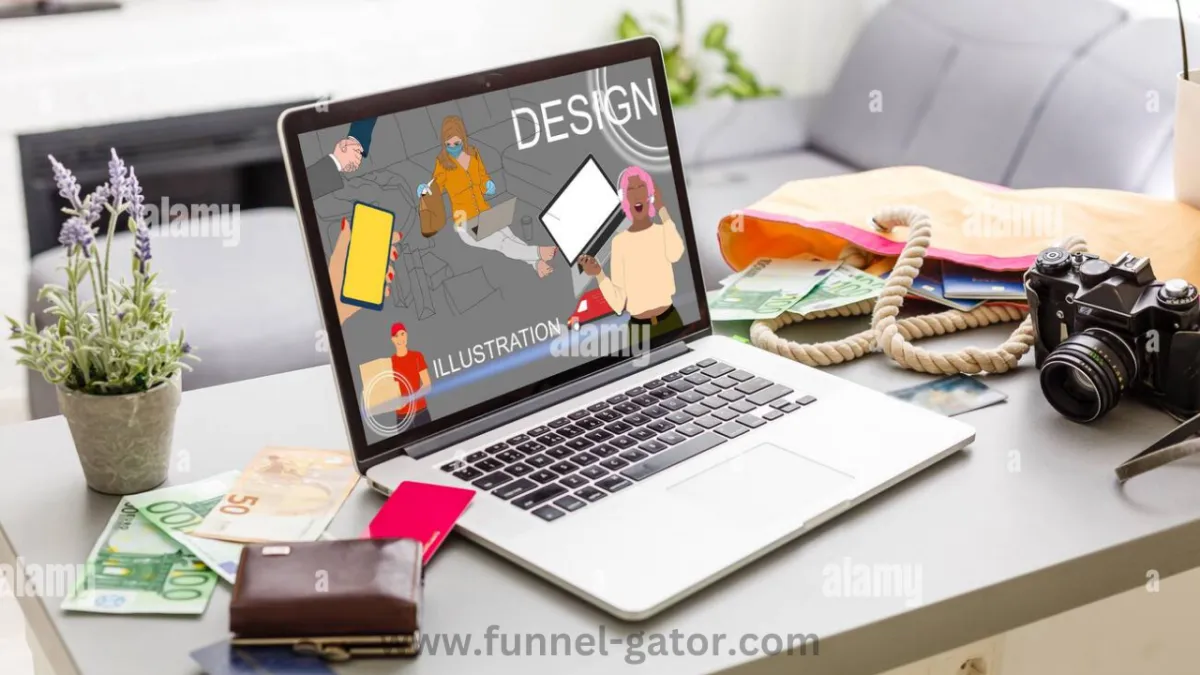
How Should a Good Process Workflow Be Designed to Reduce the Risk of Contamination
When it comes to contamination control, especially in sensitive environments like pharmaceutical manufacturing, food processing, healthcare, or cleanroom environments, a well-designed workflow can mean the difference between safety and disaster. It’s not just about ticking boxes — it's about protecting people, products, and reputations.
So, how do you build a process workflow that minimizes contamination risk while staying efficient and compliant?
Let’s walk through it together, step by step, using plain language, real-world logic, and a splash of storytime along the way.
🚧 What Is Contamination and Why Should You Care?
Imagine this: you're enjoying a nice yogurt, and halfway through, you bite into a piece of plastic. Gross, right?
That’s physical contamination.
Or let’s say someone sneezed near a surgical tool before an operation. That’s biological contamination — and it can be deadly.
Whether it’s chemical, biological, or physical, contamination disrupts processes, puts lives at risk, and often results in huge losses. According to the FDA, contamination is one of the top reasons for product recalls in food and drug industries.
🧭 Step-by-Step Guide to Designing a Contamination-Free Workflow
Let’s break it down into actionable steps.
Step 1: Map the Workflow from Start to Finish
Start by visualizing your entire process, like a flowchart. Whether it's producing vaccines or bottling ketchup, mapping each step helps you understand where contamination risks can creep in.
Tools like Lucidchart or Miro are great for drawing these out.
✏️ Real-life tip: Walk through the process physically — not just on paper. You’ll often spot things you'd miss otherwise, like that dusty air vent right above the packaging station.
Step 2: Establish Clean Zones and Flow Directions
Designate specific zones for cleaning, preparation, processing, and packaging. The key is unidirectional flow — materials should only move from low-risk to high-risk zones, never the other way around.
For example, in a GMP (Good Manufacturing Practice) pharmaceutical facility, personnel move through airlocks, gown up, and only then enter sterile zones.
Learn more about cleanroom zoning here.
Step 3: Use Color Coding and Clear Signage
This is such a simple but often overlooked tactic. Assign colors to zones, equipment, or even uniforms to avoid mix-ups.
Blue mops for the lab.
Green mops for the break room.
Red = STOP (contamination zone alert!)
Trust us — even trained staff sometimes slip up under pressure. Visual cues keep mistakes to a minimum.
Step 4: Minimize Human Contact
People are the biggest contamination sources. Hair, sweat, perfume, even the air we breathe carries microbes.
Use automation and touchless systems where possible:
Sensor-activated dispensers
Automated conveyors
HEPA-filtered air systems
Consider technologies like UV-C disinfection for tools and surfaces.
Step 5: Develop and Enforce Standard Operating Procedures (SOPs)
If your SOPs aren’t written, consistent, and updated regularly — you’re in trouble.
Each action — from handwashing to equipment sanitization — must be clear and trained for. You can't rely on "common sense" when lives are on the line.
Check out this WHO hand hygiene guide — it’s a gold standard.
Step 6: Install Proper Ventilation & Air Control
Poor airflow can blow contaminants from one workstation to another. In a cleanroom, even the direction of airflow is calculated.
Laminar flow hoods, airlocks, and positive/negative pressure rooms are your best friends here.
Need a primer on airflow management? Here’s a great overview by CDC.
Step 7: Implement a Contamination Monitoring System
Detection is protection.
Introduce regular:
Surface swabs
Air sampling
Bioburden checks
ATP testing
Set up alert systems when contamination thresholds are crossed. It’s better to shut down early than issue a recall later.
Step 8: Train, Audit, Repeat
Even the best systems fail if your people don’t follow them. So, make training a regular event, not just an onboarding step.
Create a culture of safety:
Monthly drills
Surprise audits
Reward clean habits
When employees care, they notice things like a broken seal or a sticky button on a machine.
🧪 A Quick Anecdote to Drive It Home
At a large dairy plant in Wisconsin, contamination kept sneaking into the bottling line. They blamed the equipment, then the milk, then even the cows. Turns out, the janitor was using the same mop in the warehouse and the bottling area. Just one missed detail led to thousands of spoiled bottles.
After a full workflow redesign, color-coded tools, and retrained staff, they cut contamination incidents by 92% in just 3 months.
💡 Bonus: Use the Right Contamination Control Products
A good workflow is nothing without the right tools. That’s where our top-tier contamination control solutions come in.
From cleanroom wipes to sanitizing agents, antimicrobial coatings, and disposable garments, we offer scientifically tested products that meet the highest GMP and ISO standards.
👉 Explore Our Contamination Control Products
✅ Final Thoughts: Build It Right, Sleep at Night
Designing a contamination-resistant workflow isn’t a one-time project — it’s a commitment. But by focusing on:
Flow direction
Clean zones
Human behavior
Monitoring and training